Virtual diving - Fraunhofer IGD develops digital underwater technologies in Rostock
(Rostock) Even the dark side of the Moon has been studied more than the depths of the oceans. At its Rostock location, Fraunhofer IGD is developing trendsetting digital underwater technologies to help the study of the ocean take a major step forward.
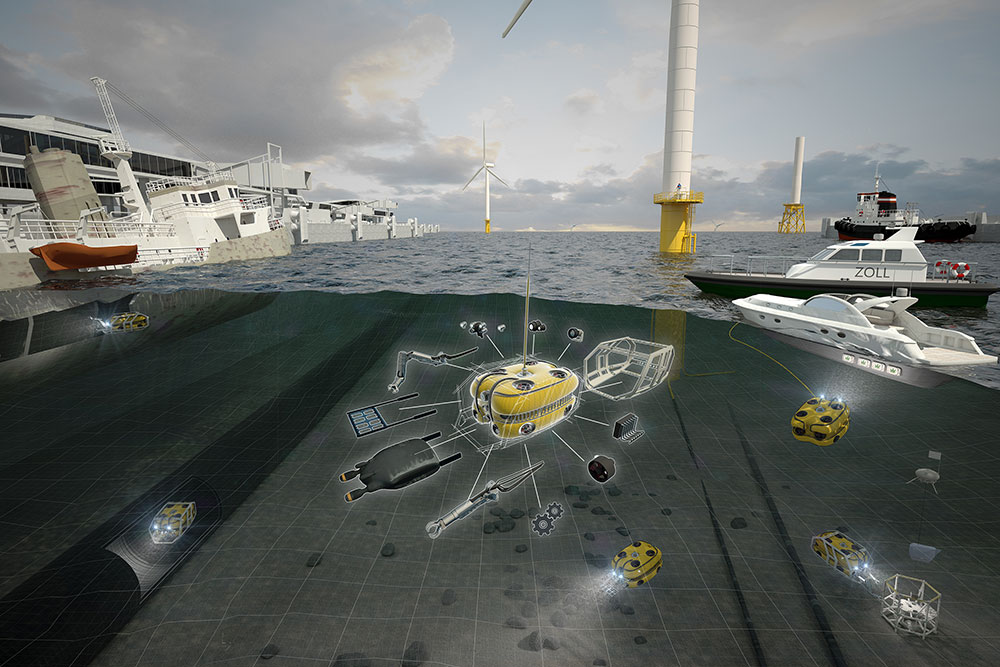
Underwater research is laborious, since humans usually only have access under very difficult conditions and sometimes even need to accept a certain level of personal risk. This is why remotely operated vehicles (ROVs) or autonomous underwater vehicles (AUVs) are used. Equipped with submersible cameras and sensors, they provide valuable recordings and information researchers would not be able to get without them. In the Baltic Sea, these underwater robots see a variety of use, from maintaining offshore installations to exploring shipwrecks for archeological purposes, to detecting old munitions.
Smart camera for a new generation of ROVs
As part of the “MiroBase” project funded by the Federal Ministry of Education and Research, a number of partners -- including the Fraunhofer Institute for Computer Graphics Research IGD in Rostock -- are developing a functional prototype for a new generation of underwater vehicles that is expected to be completed by the end of 2020. This generation will be more maneuverable, more flexible, and have better technology than the vehicles in use today. Using two different test systems -- a standard ROV and a specially developed bionic vehicle modeled after the sea turtle -- a modular vehicle system will be developed that, equipped with a multitude of functions, can be used for a broad range of applications. It is this lack of multifunctionality that is the drawback of today’s standard ROVs. For the project, Fraunhofer IGD is developing a smart camera that enhances underwater images in real time, making the picture -- taken by the underwater vehicle during a dive -- considerably clearer. At the same time, its algorithms can independently detect objects and transmit the improved image directly to the vehicle operator along with other information. This makes it so the pictures can be used not just for post-dive analysis, as is currently the case, but also to collect valuable data during the dive to help decide on the next steps. In cooperation with the state association for underwater archeology in Mecklenburg-West Pomerania, test dives will be conducted in the coming weeks on shipwrecks in the Warnow river and Baltic Sea that will put standard ROV systems through the paces in order to derive requirements for more detailed control mechanics and test the camera system’s current state of development.
Making visible the invisible -- with eyes that can hear
To gather usable visual information even at extreme depths, underwater vehicles need powerful sensor and sonar systems that replace the eyes and ears. Established systems based on optical or acoustic sensors have significant shortcomings even today, often only providing sufficiently accurate and robust images of the underwater situation, such as seafloor structures, cable or pipeline installations, organism colonization or raw material distribution, when combined with different types of systems and special carrier vehicles. Fraunhofer IGD is also working with partners on a solution to this problem: An innovative acoustic 3D imaging and surveying system is being developed as part of the “Acoustic Eye” project funded by the Federal Ministry for Economic Affairs and Energy. Bionic findings from how bats and dolphins process signals make it possible to obtain and analyze in real time complex acoustic spatial and spectral information. With this data processing and live visualization, ROV operators can wear smartglasses that allow them to detect the composition of the seafloor and in some instances even go below the visible surface. This can not only help detect shipwrecks faster but also inspect cables or pipelines for leaks or be used to probe natural manganese deposits. The latter currently requires time-consuming manual measuring of the area and subsequent soil samples. As a smart sensor system in underwater vehicles, the “acoustic eye” can take over and make easier the measuring, detection and precise definition of manganese deposits.
Lack of testing options under real conditions
Whether developing new control units or sensor systems for vehicles, testing image processing algorithms or testing the latest protective materials for offshore installations, all underwater technology has one thing in common: So far it has not been possible to test new developments under real conditions. Current, salinity, visibility and every other natural factor in the open sea can only be artificially reproduced in test basins and pressure tanks to a certain degree. All this will change with the Digital Ocean Lab, which will be established off the coast of Nienhagen and managed by Fraunhofer IGD, offering both research and industry an ideal environment for practical testing under real conditions with its numerous test areas. It will be the starting point for Rostock’s large-scale project, the “Ocean Technology Campus”, where various players in the underwater environment from science and business will have an ideal setting for sharing technological know-how. A research group consisting of various Fraunhofer institutes will already begin its work in the fall of 2019 at the fishing port in Rostock. The Digital Ocean Convention Rostock on August 9, 2019, which will be attended by representatives from government, research and industry, will serve as the symbolic kick-off of the expansion work for the Digital Ocean Lab.