Automated quality control makes high-vis clothing safer
High-visibility or “high-vis” clothing provides many people safety in their day-to-day work. Fraunhofer IGD has paired with textile service provider MEWA to develop an automated system for inspecting the quality of this clothing faster and more reliably, and thereby guarantee safety. Both companies have filed a joint patent for the system.
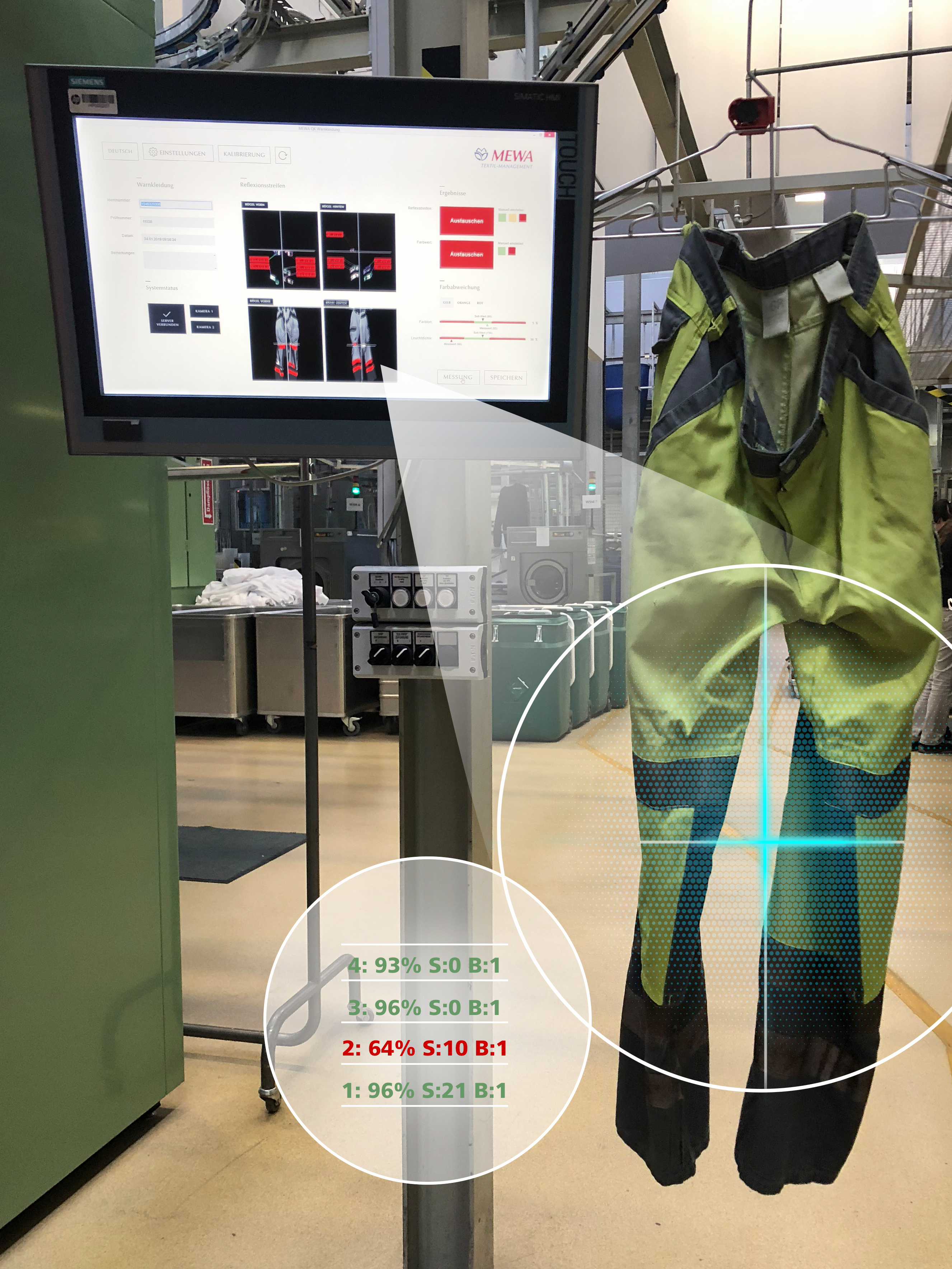
High-vis and protective clothing, like the kind worn by road workers, must meet certain standards prescribed by law for the safety of the wearer. Employers are liable for meeting these legal safety standards. On behalf of MEWA, the Fraunhofer Institute for Computer Graphics Research IGD has developed a system to automate and optimize quality testing.
Integrated optical quality control
Fraunhofer IGD has developed its quality control system with the assistance of MEWA Textil-Service AG and it will be used daily at two sites starting in 2020. After being washed and dried, the articles of clothing run through a special photographing box on hangers and pictures are taken of the front and back. Fraunhofer software analyzes these pictures in real time and sends to the result to control software, which sends the clothing to other stations in the quality control process. The results of the inspection are saved in the system¾a valuable collection of data that is made available to MEWA in order to analyze and optimize the system as well as internal processes, such as the washing process.
Faster and more precise inspection
The high-vis clothing is inspected manually for quality by qualified employees. They inspect the washed articles of clothing for a number of aspects, including brightness and colorfastness of the high-visibility color as well as the integrity of the reflective strips. The automated solution by Fraunhofer IGD can assist employees with this visual inspection while speeding up the process at the same time. “With the help of the automated analysis, we can ensure to an even greater degree and with greater precision that the high-vis clothing meets strict safety standards even after being washed,” said Uwe Schmidt, head of engineering at MEWA. At MEWA’s locations in Schönbuch near Stuttgart and Gross Kienitz near Berlin, Fraunhofer IGD’s system is now being used in trials, with implementation at more locations being planned.
Inspection system is applicable to other industries
Fraunhofer IGD’s inspection system is available for implementation as a software module. This technology could also support other industries: Automated returns classification for the mail-order trade or use in textile recycling would be conceivable, though the technology would need to be seamlessly integrated into existing systems and processes. The development team at Fraunhofer IGD is currently working on quality controls that use not only photographs but also video recordings as well as on analyzing the recordings in real time. The significantly increased number of product views will cover every aspect of the inspection with even greater precision.