MARQUIS
Fraunhofer IGD develops AI-based component inspection for faster changeover times
MARQUIS software from Fraunhofer IGD facilitates the mobile inspection of components in real time. Customers in the automotive sector benefit from shorter changeover times, from user-friendly operation and from lower costs as a result of less downtime on production lines. The developers will be showcasing this software package for mobile quality inspection at the CONTROL trade fair (early May) and at HANNOVER MESSE (early June).
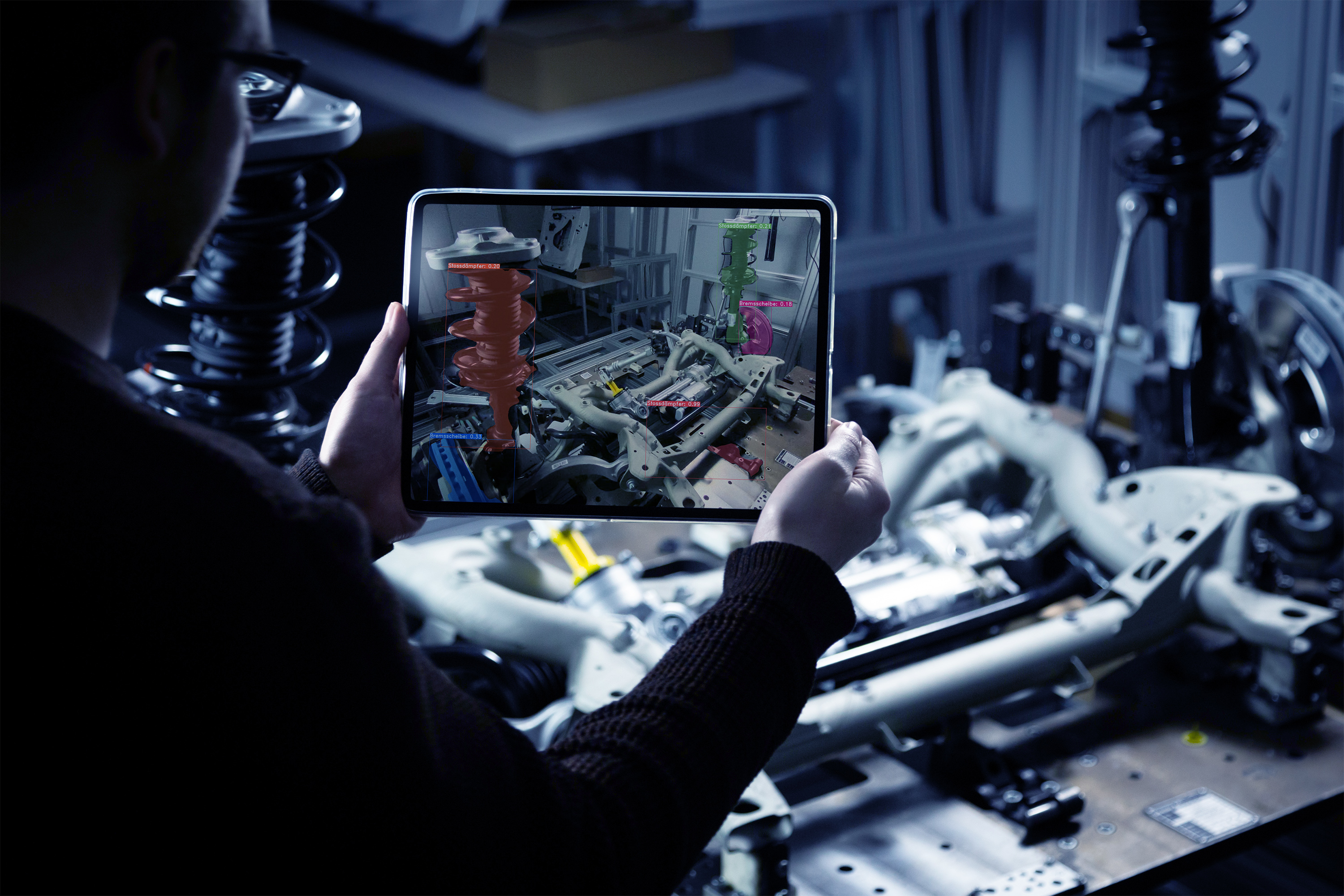
Darmstadt: A missing screw, a crooked suspension strut or a wrench left lying around – these are just a few of the things that can go wrong on production lines in the automotive sector, which is why efficient and user-friendly inspection systems are considered essential. MARQUIS software combines augmented reality with machine learning methods for the purpose of automated inspection in real time.
“The software does not need to work with actual photos in order to train the Artificial Intelligence and to mark inspection cases,” explains Holger Graf, head of department at the Fraunhofer Institute for Computer Graphics Research IGD. “Instead, it uses synthetically generated images from the CAD model.” The software then compares the CAD specifications with the components as presented. The system is trained to recognize these without ever having seen real assemblies before. MARQUIS is remarkable for being fully automated – a feature that reduces lead time from one or two weeks to just a few days. Users in the automotive sector benefit from faster changeover times and correspondingly more drop tests per day. Corrections can be made directly without the need for the entire production line to be brought to a halt. This reduces cost-intensive downtimes that can occur with conventional stationary test arrays.
Flexible component inspection in the production process
MARQUIS is suitable for use not only at stationary inspection stations, but also at other locations. With the aid of smartphones, tablets or even AR glasses, employees can inspect the components as part of a dynamic process. “The system identifies the component to be inspected, its positioning and whether it deviates from the target dimensions,” adds Graf. User-friendly visual feedback flags up any errors in the assembly detected by the software – the component then lights up red. The AI‑based software is also capable of recognizing deformable objects such as hoses.
With the latest generation, it is even possible to call up experts remotely. These specialists can then offer remote support to the individual on site performing the inspection. In addition to checks on the production line, the software is also of immense help to automotive manufacturers in the inspection of incoming or outgoing goods. Where random sample checks were previously the norm, every single component can now be scrutinized at an inspection bench.
The development team will be presenting the MARQUIS software package at the CONTROL international trade fair for quality assurance (3rd ‑ 6th May), and at HANNOVER MESSE (30th May ‑ 2nd June). It is the result of a project partly funded by the German federal state of Hesse in the context of the Löwe program (project number 928/20-85), which ends in May. Fraunhofer is working closely with the spin-off Visometry to develop the prototype into a market-ready product.
Further information:
More information on this and all other Fraunhofer IGD exhibits at HANNOVER MESSE can be found at: https://fh-igd.de/HMI