Rapid prototyping in 3D printing: New pipeline brings increased efficiency and robustness
A new technique is increasing the efficiency of 3D printing at native device resolution, especially with multi-material jetting, aka Polyjet, printers. With the Cuttlefish® 3D printer driver, even the finest textures can be reproduced with efficiency and robustness at reduced file size – a decisive factor in any large print job. The results will be presented at SIGGRAPH 2021.
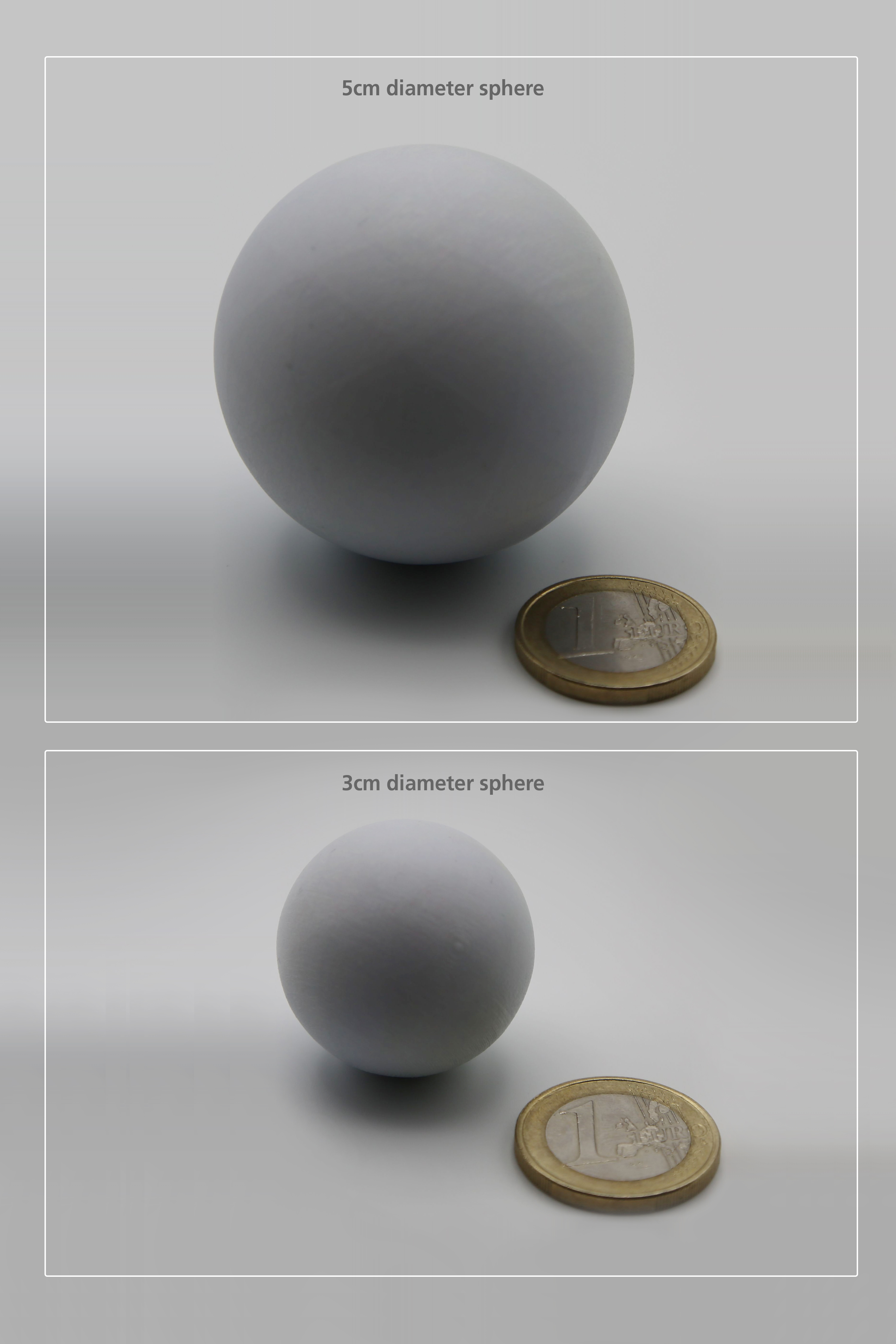
The level of resolution and accuracy achieved by the hardware in the current generation of 3D printers allows for ever more realistic reproduction of surfaces. At the same time, factors such as file size, transmission and processing time add a further layer of complexity. This is due to the high number of polygons needed to approximate the desired surface, especially for large print sizes.
Researchers of the 3D Printing Technology team at Fraunhofer IGD recently published a paper – Displaced Signed Distance Fields for Additive Manufacturing – proposing a solution to this dilemma. The clever thing about the technique is the way it splits the surface representation into macroscopic and mesoscopic parts, and uses the latter to reproduce both fine-scale surface detail and smoothly curved surfaces. This results in an efficiency advantage that increases with scaling, especially for large print jobs, compared to refining the surface tessellation using flat primitives. The paper was accepted to SIGGRAPH 2021, the most prestigious event for computer graphics. The conference will be held virtually August 9-13, the paper will be presented August 13, 12pm - 1pm PDT. The solutions presented in the paper have already found an application in the Cuttlefish® 3D printer driver.
The new method in detail

At the heart of the algorithms described are so-called “displaced signed distance fields”, which augment the near ubiquitous signed distance field representation with a displacement field, specifying the offset from the input approximation to the true surface. This implicitly encodes smoothly curved or fine-detailed surfaces with respect to a coarse tessellation. For 3D printing, the models generated by human operators or by a scanning pipeline must be converted into polygon meshes. For a fixed print size, a fixed number of polygons suffices to print the object at the precision of the printer, but for larger print sizes, they must more finely tessellated, potentially with many more polygons.
The example of a plain sphere illustrates the problem: the printed sphere may appear round with a certain number of polygons, but if the object is printed larger with the same polygon mesh, the sphere no longer appears round. Displaced signed distance fields encode the difference between the piecewise flat input mesh and the true surface of the sphere, at the precision of the 3D printer.
Displaced signed distance fields represent the surface of the shape implicitly, allowing for volumetric regularization of the implicit function and robust computation from incomplete or self-overlapping surface data. This is especially relevant in 3D printing, as information processed in situ cannot be corrected. The new algorithms of the Cuttlefish® 3D printer driver thus facilitate highly detailed and smooth surfaces from low-poly meshes, in a robust, streaming compatible approach.
