Qualitätscheck mit Augmented Reality
Automatisierte, Computer-Vision-gestützte Systeme objektivieren die Qualitätskontrolle in der Automobilproduktion. Das Fraunhofer IGD präsentiert auf der Messe CONTROL ein Verfahren, das den IST-Bauzustand erfasst und mit dem SOLL-Bauzustand laut CAD-Daten abgleicht – in Echtzeit.
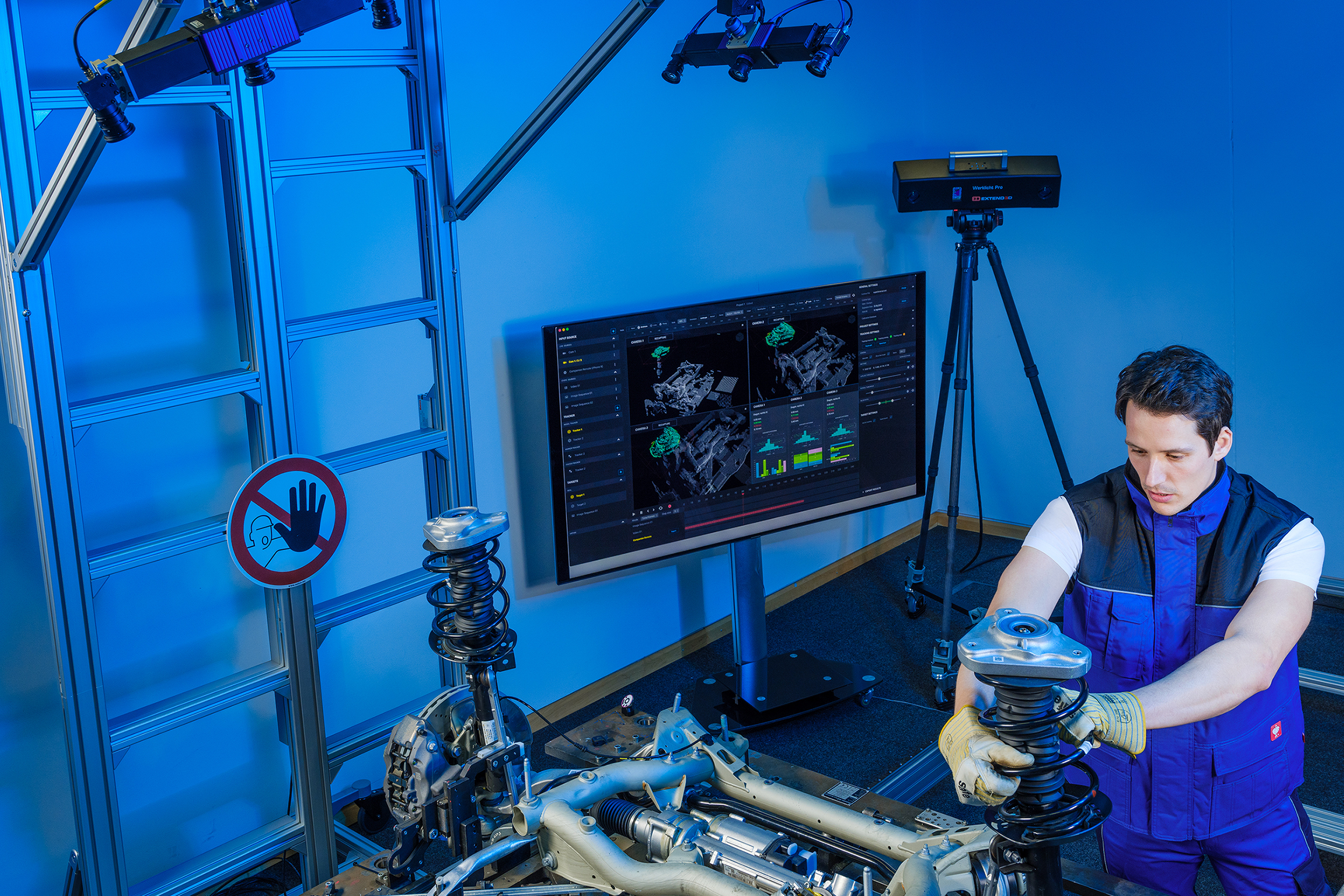
(Darmstadt/Stuttgart) Wenn ein Bauteil aus mehreren Komponenten zusammengesetzt wird, ist ein millimetergenaues Arbeiten für die Qualität des Endproduktes entscheidend. Die fertigende Industrie wie die Automobilindustrie bedarf einer verlässlichen Qualitätskontrolle, die sich dennoch nahtlos in den Fertigungsprozess eingliedert. Das Fraunhofer-Institut für Graphische Datenverarbeitung IGD hat gemeinsam mit der Daimler AG, der TIGRIS Elektronik GmbH und der Ensenso GmbH im Rahmen des Projektes »Scrutinize3D« ein vollautomatisches System zur optischen Qualitätssicherung im Fahrzeugbau entwickelt. Ziel war die Etablierung einer Methodik, die vollautomatisiert eine Qualitätskontrolle für zusammengesetzte Bauteile an der Produktionslinie durchführt. Das Projekt wurde Anfang 2019 abgeschlossen und das System ist nun einsatzbereit – im Automobilbau oder anderen Bereichen der fertigenden Industrie.
Live-Abgleich mit CAD-Daten
Konkret sieht das folgendermaßen aus: An einer Produktionslinie werden Kameras fest verbaut. Diese nehmen die von Robotern oder Arbeitern zusammengebauten Teile auf. Das Produktionskontrollsystem prüft mithilfe der vom Fraunhofer IGD integrierten Algorithmen, ob alle Bestandteile vorhanden sind, ob die richtigen Teile verbaut wurden und ob alle für den nächsten Verarbeitungsschritt korrekt positioniert sind. Erkennt das System eine Abweichung, stoppt es das Band und signalisiert den Werkern die Notwendigkeit zum Eingreifen. Der entscheidende Vorteil gegenüber vergleichbarer und am Markt etablierter Systeme: Es findet ein Live-Abgleich mit den CAD-Daten, also den ursprünglichen Konstruktionsdaten, statt. Das macht den Qualitätscheck nicht nur besonders genau, sondern auch schnell. Alternative Lösungen arbeiten auf Basis von Referenzbildern, das heißt, dass Kamera und System viele Hundert Beispielbilder brauchen, um Abweichungen von der Norm zu erkennen. Das bedeutet ein langwieriges Anlernen, das jedes Mal wiederholt werden muss, wenn sich die Produktvariante oder einzelne Bauteile ändern. Auch hier zeigt das Fraunhofer-System seine Stärken: Ändern sich Fahrzeugkomponenten und damit die Anforderungen an die Qualitätsprüfung, greift es einfach auf eine andere CAD-Datenbasis zu. Damit ist es sehr flexibel und schnell in neuen Situationen einsatzbereit. Die synchronisierten Kameras, welche die Bauteile erfassen, werden für das Messeexponat im Augmented-Reality-Prüftisch verbaut, um die Qualitätskontrolle und den SOLL-IST-Abgleich zu unterstützen.
Qualitätssicherung to-go dank AR
Auf der Messe präsentiert das Fraunhofer-Team ebenso seine Entwicklung anhand der mobilen Prüfvariante. Ein Prüfteil wird von der Kamera eines Tablets erfasst und in Echtzeit mit den CAD-Daten abgeglichen. Mittels Augmented Reality (AR) werden nun die fehlerhaft verbauten oder fehlenden Bestandteile visualisiert. Das ermöglicht eine Qualitätsprüfung auch außerhalb des Werkes – bei bereits ausgelieferten Kundenproduktionen oder Zulieferern. Der Messe-Showcase mit Kameraprüftisch und Tablet demonstriert außerdem, dass das Prüfsystem flexibel funktioniert und an alle Gegebenheiten anpassbar ist – von der mobilen Tablet-Kamera bis zu 3D-Prüfkamerasystemen an der Produktionslinie.