AI-based process control, suitable even for smaller batch sizes
In the automotive sector, in plant construction and in tool manufacture, it is essential to have effective quality assurance measures in place – errors that occur during production are too costly to tolerate. One solution is Marquis, a system developed by Fraunhofer IGD to provide AI- and AR-based live assistance during the assembly process. At this year’s Control, trade visitors will have the opportunity to test the AR assembly workstation for themselves.
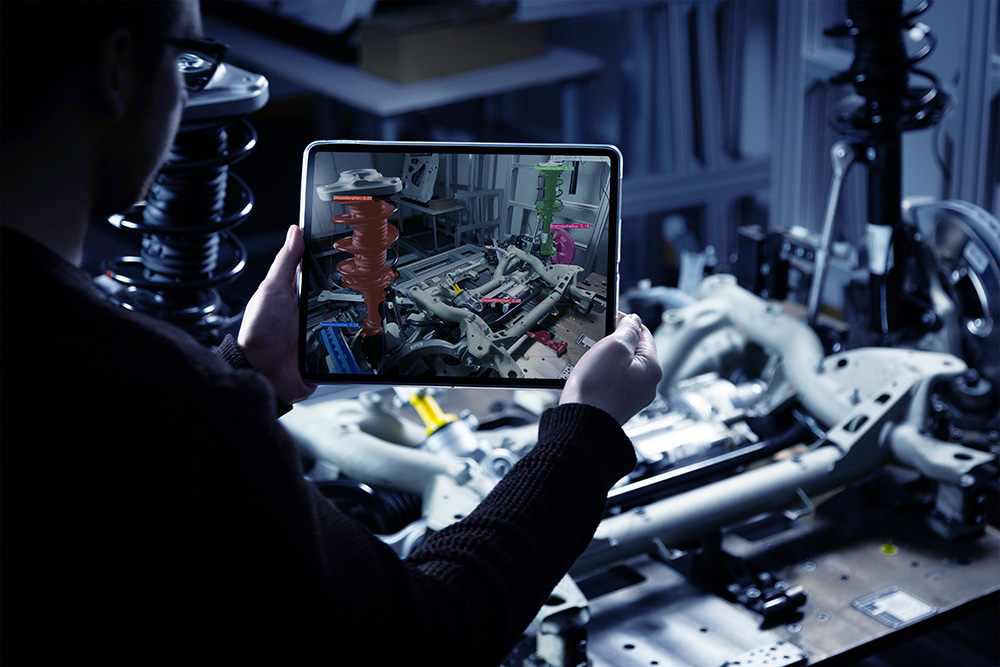
Darmstadt: Industrial assembly processes can vary greatly, sometimes involving small batch sizes, prototypes or operating resources. Fraunhofer Institute for Computer Graphics Research IGD has developed Marquis, a system for optimizing quality management. The solution combines artificial intelligence (AI) with augmented reality (AR) and offers visual inspection during the ongoing assembly process. It guides workers through assembly steps, flags up components that have been incorrectly assembled and advises on the correct method of assembly.
By recording each individual work step, the system can also render additional documentation superfluous. Whether supplied with image verification only or with an additional comment field, the Fraunhofer solution reduces the time and effort required for all-round quality assurance.
Avoiding errors in the assembly process
“Marquis is an add-on solution for industry that can be integrated directly into production processes and is ready for use at short notice,” says Holger Graf, Head of the Virtual and Advanced Reality Department at Fraunhofer IGD. “We can respond to the respective individual requirements and embed Marquis deep into the customer’s system as appropriate.”
The AI for digital assembly control is trained using computer-generated images based on CAD models. Marquis employs four cameras that are pointed at the area in which the employee is working. These detect the various components. A screen attached to the side as an AR output unit shows if a component has been incorrectly selected or installed. “Up to now, users have tended to prefer tablets to AR glasses because they find them uncomfortable to wear,” explains Graf. However, with optimized AR glasses, output via a head-mounted unit is also conceivable in the future.
Your opportunity to test Marquis at Control
Production effort in an industrial context are always relatively high wherever fully automated series manufacture is not viable. “Learning the correct assembly procedure takes time, and errors occur more readily due to the lack of an established routine,” says Graf. “Marquis ensures that time and effort is minimized and thus supports cost-efficient assembly processes.” At this year’s Control trade fair, visitors will have the opportunity to test the system for themselves on an assembly workstation equipped with Marquis at the Fraunhofer IGD stand.
Developed by Fraunhofer IGD, Marquis uses innovative AI-based object detection in combination with advanced tracking algorithms that are already in use in the automotive sector. These algorithms were likewise developed at Fraunhofer IGD and are now managed and marketed by the spin-off Visometry GmbH. Marquis goes a decisive step further, offering automated quality control and intuitive assembly guidance. The solution can also be used in training contexts. Holger Graf: “Marquis is a valuable aid wherever things need to be assembled.” The modern, digital way of working could be an important incentive for young people to learn a trade.
Further Information
- To our presentation and exhibits at Control 2024 (igd.fraunhofer.de)